Press Release
World's First Aircraft with Large Scale Riblet Coating Introduced on International Routes
- Launching the First Fuel Efficiency Validation on a Boeing 787-9 -

(Joint Release)
January 10, 2025
Japan Airlines Co., Ltd.
Japan Aerospace Exploration Agency
O-WELL CORPORATION
Japan Airlines Co., Ltd. (Headquarters: Shinagawa-ku, Tokyo; President: Mitsuko Tottori; hereinafter "JAL"), the Japan Aerospace Exploration Agency ( Headquarters: Chofu City, Tokyo; President: Hiroshi Yamakawa; hereinafter "JAXA"), and O-Well Corporation ( Headquarters: Nishiyodogawa-ku, Osaka; President: Yasuharu Kawato; hereinafter "O-Well") have applied riblet-shaped coating to the majority of the fuselage of a Boeing 787-9 aircraft (JA868J) for the first time in the world. Additionally, this marks the first global use of an aircraft with riblet coating to be operated on international routes, with the inaugural flight scheduled for mid-January 2025.
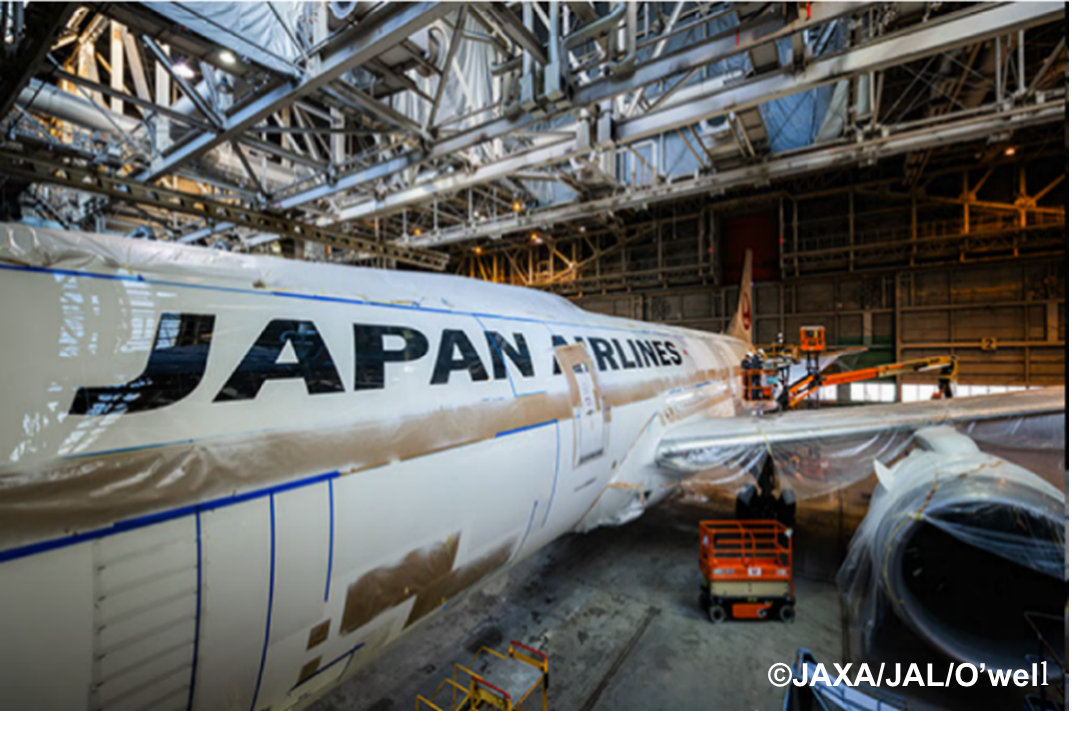
Riblet Application Work Scene
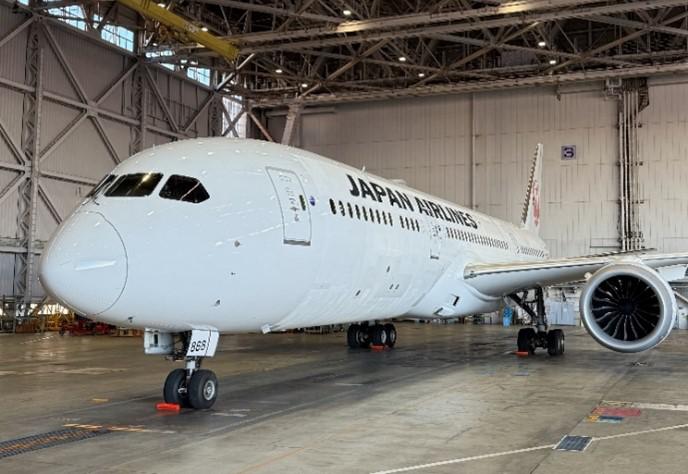
Boeing 787-9 with Riblet Coating (JA868J)
JAL, JAXA, and O-Well are promoting the decarbonization of aircraft industry As part of this effort, they have applied riblet (*2) -shaped coating to the aircraft's exterior using the Paint-to-Paint Method (*1), a technology continuously improved by O-Well, and have been validating its durability and fuel efficiency improvement effects. Since July 2022, they have been testing the durability of the riblet-shaped coating on JAL's domestic aircraft (Boeing 737-800), and since November 2023, they have been confirming the fuel efficiency improvement effects by applying the coating to a large area of the fuselage bottom (*3) (*4). The Paint-to-Paint Method, which applies riblet shapes directly to the paint film, is expected to reduce weight and improve durability compared to riblet processing using decals or films.
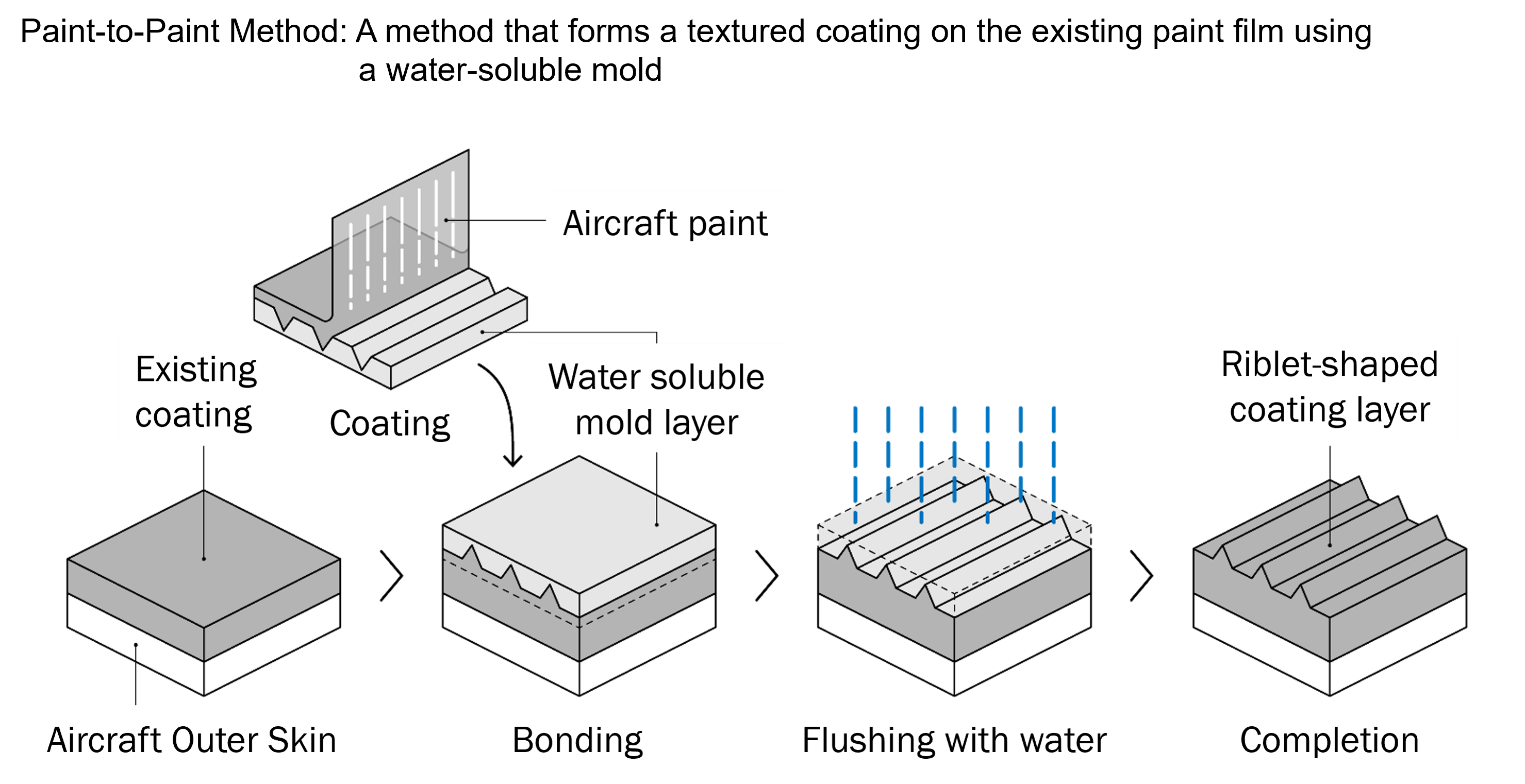
This time, wind tunnel tests and numerical analyses by JAXA confirmed the drag reduction effect on international aircraft (equivalent to a Boeing 787-9), and the development of a riblet coating system by O-Well that can accommodate larger aircraft has enabled the expansion of the application area to the upper fuselage of international aircraft . Long-haul flights on international routes are expected to yield further fuel efficiency improvements.
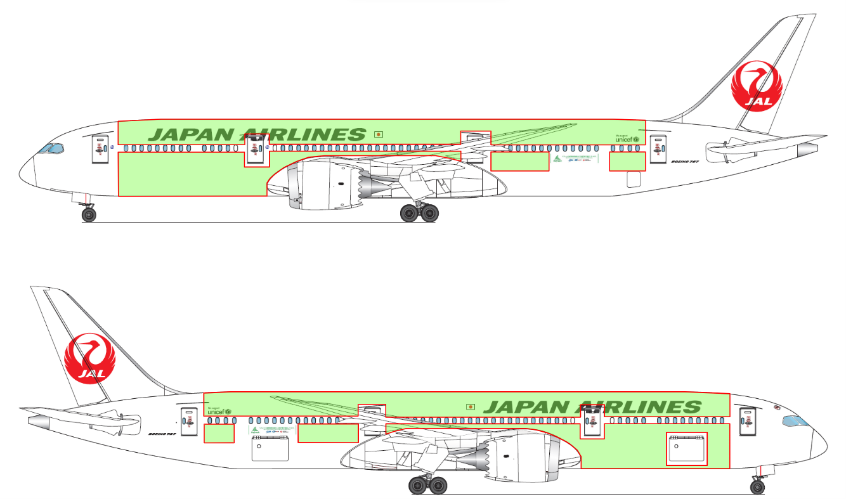
Riblet Application Area
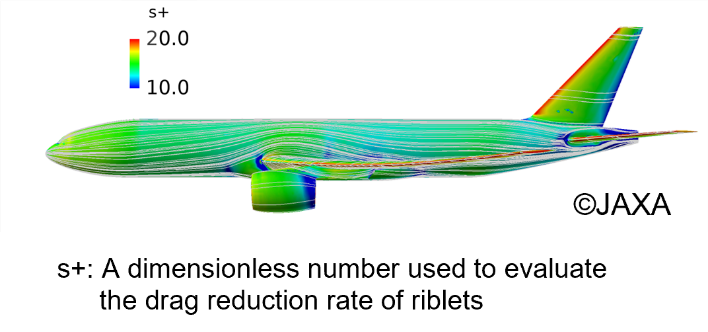
Estimated Drag Reduction Analysis Using Riblets on a Boeing 787-9 Equivalent Aircraft (s+ Distribution and Surface Streamlines) (*5)
In the aircraft with the newly applied coating, the drag reduction rate during cruising is 0.24%, which is expected to result in an annual reduction of approximately 119 tons of fuel consumption and about 381 tons of CO2 emissions (*6). This is equivalent to the annual CO2 absorption of approximately 27,000 cedar trees.
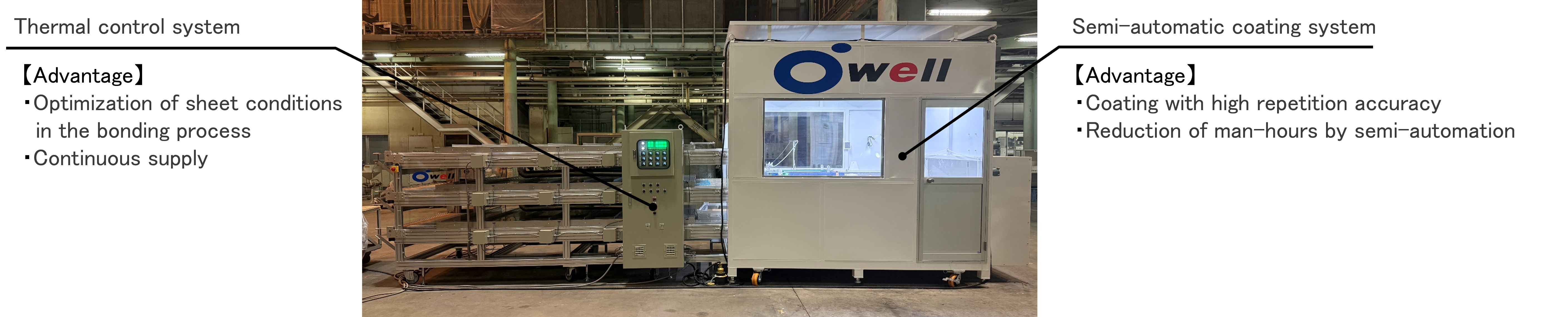
Moving forward, JAL, JAXA, and O-Well will continue to work together to promote the decarbonization of aircraft by validating the durability, aesthetics, and fuel efficiency improvement effects of the large-scale riblet coating on long haul international flights, and by expanding the scope of application.
(*1) Paint-to-Paint Method: A method that forms a textured coating on the existing paint film using a water-soluble mold.
Joint patent by O-Well and JAXA (Patent No. 6511612).
(*2) Riblet: Fine groove structure inspired by the shape of shark skin, which reduces water resistance. By forming a fine groove structure on the aircraft's exterior panel along the air flow during flight, drag can be reduced.
(*3) March 07, 2023 Press Release: "JAL, JAXA, O-Well, and Nikon Conduct Flight Test with Aircraft for which the World's First Riblet Shape was Applied over External Paint"
https://press.jal.co.jp/en/release/202303/007277.html
(*4) November 30, 2023 Press Release: "JAL Initiates Flight Test to Measure the Fuel Efficiency Improvement Effect by Applying Riblet Shapes in a Large Area on Aircraft "
https://press.jal.co.jp/en/release/202311/007781.html
(*5) An example of the estimated drag reduction effect when riblets are applied to the aircraft. The dimensionless number s+ is used to evaluate the drag reduction rate of riblets, and it is generally considered that the drag reduction rate is maximized when s+ is around 15-17. The angle between the riblet groove direction and the surface streamline direction is also considered in the estimation.
(*6) The predicted effect of flying the route for one year, calculated based on the drag reduction rate estimated by JAXA and the fuel consumption on the Narita-Frankfurt route over the past year.
END